Research Center
Metals and Alloys Processing and Protective Coatings Center
About the center
Our Center conducts scientific, research and development, technological, design, and training activities in the field of heat treatment and thermo-chemical treatment of metals and alloys. We provide solutions for industries such as automotive, transportation, metal, tooling, defense, mining, and others. Our team also engages in activities related to the application of eddy current methods and the development of equipment and probes, as well as automated research stations. Our goal is to reduce losses caused by corrosion by promoting anti-corrosion technologies and developing or verifying new technological solutions for metal, polymer, composite, and ceramic coatings.
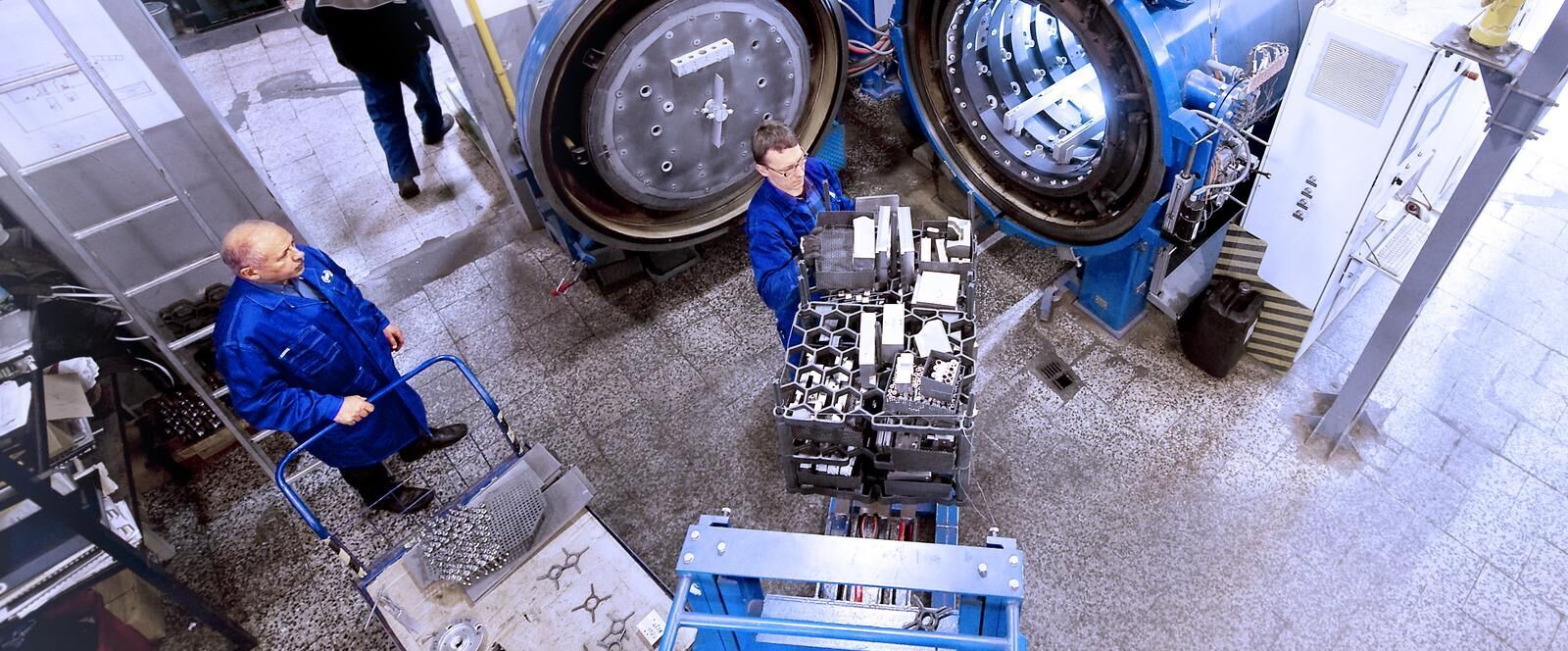
Research Groups and Laboratories in the Metal and Alloy Processing and Protective Coatings Center:
- Research Group for Heat Treatment
- Heat Treatment Services Section
- Research Group for Thermo-Chemical Treatments
- Research Group for the Design of Process and Control Equipment
- Mechanical Properties of Materials Laboratory
Metals and Alloys Processing and Protective Coatings Center
Our Focus:
- R&D for Industry: Development of heat and thermo-chemical treatment technologies on client equipment.
- R&D for Industry: Development and manufacturing of apparatus, control and measurement systems, and eddy current probes for non-destructive testing; developing non-destructive testing methodologies and adapting them to examined components.
- Technological services in atmospheric, vacuum, and cryogenic heat and thermo-chemical treatment performed on client charges.
- R&D for Industry: Designing and manufacturing non-standard equipment for atmospheric and fluidized bed heat and thermo-chemical treatment.
- Modernization and design of technological stations for certain heat and thermo-chemical treatment processes.
- Activities in heat, thermo-chemical, atmospheric, vacuum, and cryogenic treatments conducted for subsidy works and R&D projects in the Center's and Institute's Research Groups.
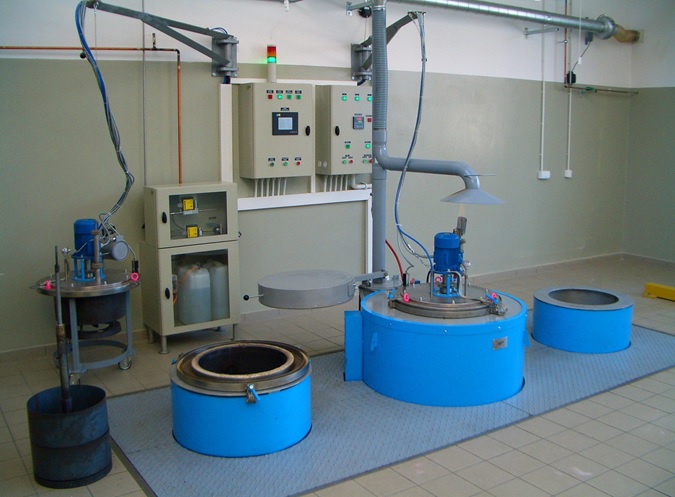
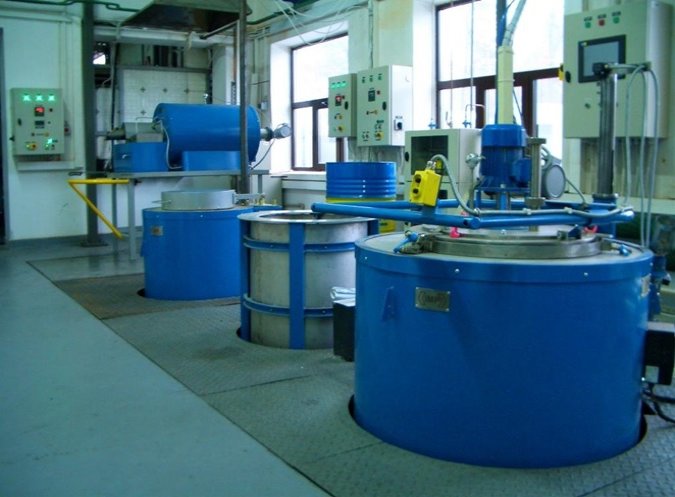
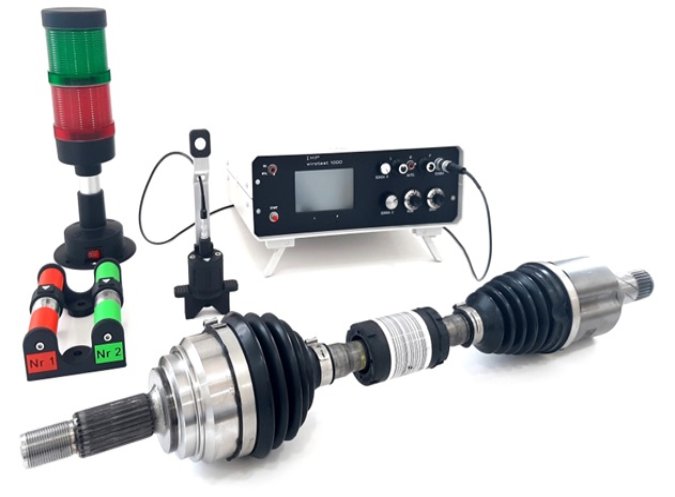
Metals and Alloys Processing and Protective Coatings Center
Research Group for Heat Treatment
- New heat treatment technologies for metals and alloys, with a focus on thermal processes in vacuum, fluidized beds, and protective atmospheres.
- Technologies for freezing (including cryogenic) combined with heat treatment.
- New metal joining technologies (especially vacuum brazing).
- Highly specialized services for industry, including expertise and studies in the area of activity, as well as material and technology selection.
- Realization of technological processes in the field of heat and thermo-chemical treatment; atmospheric, vacuum, fluid, and cryogenic on client charges: annealing, hardening, freezing, tempering, carburizing, nitriding, carbonitriding, nitrocarburizing, oxynitriding, oxidation.
- New! – Low-Pressure Carburizing (LPC)
- LPC offers benefits unattainable in conventional carburizing, such as high repeatability and uniformity of the carburized layer, no surface oxidation, and the ability to carburize at higher temperatures.
- Realization of technological processes in low-pressure carburizing LPC in a 15VP-446 type furnace, allowing for treatment charges of up to 200 kg.
Our specialists are pleased to answer all your questions.
Contact us for more information.
Sylwester Jończyk
Research Group for Heat Treatment
Paweł Tomczyk
Heat Treatment Services Section
Metals and Alloys Processing and Protective Coatings Center
Research Group for Thermo-Chemical Treatment
- Design and implementation of nitriding processes (gas and plasma), PVD, and hybrid processes (combining with other bulk and surface treatments);
- Performing technical assessments and evaluations of layers and coatings produced by nitriding, carbonitriding, thermal spraying, and PVD processes.
- Development of technological foundations for production lines and equipment for gas nitriding, plasma nitriding, thermal spraying, and PVD.
- Developing parameters and implementing thermal spraying of metal and cermet coatings for regeneration, decoration, and tribological and anti-corrosion protection.
- Training activities in nitriding technologies and obtaining metallizer work qualifications in thermal spraying technology in accordance with PN-EN ISO 14918.
- Thermal sprayinge – is a process where coating material in the form of wire, powder, rod, or filament is heated to a plastic or molten state and then sprayed with a gas stream, most often compressed air, onto a prepared surface. The factor causing the coating material to melt is the heat of an oxy-fuel torch, electric arc, or plasma. Particles, upon striking the substrate, deform and layer upon each other to form a coating. At Łukasiewicz – WIT, we use arc spraying, supersonic flame spraying with powder and wire.
Benefits:
- Simple technological process,
- Ability to use equipment on any production scale, both non-automated and fully automated;
- Ability to apply coatings from materials with different chemical compositions or from a mixture of multiple materials;
- Low thermal spraying temperature avoids the undesirable structural changes and deformations in the substrate material;
- Coatings can be applied to metal, wooden, glass, ceramic, plaster, textile objects, etc., in the engineering, marine, electrical, chemical, food industries, construction, and transportation.
Applications:
in the machinery, shipbuilding, electrotechnical, chemical, food, construction, and transport industries.
Training and implementation of thermal spraying technological processes on client parts.
Our specialists are pleased to answer all your questions.
Contact us for more information.
Piotr Wach
Research Group for Thermo-Chemical Treatments
Metals and Alloys Processing and Protective Coatings Center
Research Group for the Design of Process and Control Equipment
- Development and manufacturing of apparatus, control, and measurement systems, as well as probes for non-destructive testing using eddy currents;
- Development and manufacturing of non-catalog equipment for heat and thermo-chemical treatment, as well as modernization of existing stations;
- Rapid prototyping using modeling, scanning, and 3D printing tools.
- Development of dedicated control and measurement systems and probes for non-destructive testing using eddy currents, designed for a specific object and test purpose.
- Non-destructive testing using eddy currents for detecting discontinuities, assessing changes in material microstructure, and measuring layer and coating thickness.
- Scanning and 3D printing services.
Shot Peening
Technology in dynamic surface treatment to strengthen the surface parts of aerospace, machinery, and construction components and improve resistance to material fatigue. The treatment is conducted in a chamber for peening hard and superhard materials PEEN-IMP (patent PL 2047180).
Benefits:
- Reducing the harmful impact of surface defects (decarburization, microcracks);
- Mitigating the effects of stress concentrators, both constructional and technological;
- Strengthening machine parts with developed and curvilinear surfaces (gear wheels);
- Increasing durability and preparing surfaces for paint coatings in one operation;
- Increase in durability or fatigue strength from 25% to 100%.
Our specialists are pleased to answer all your questions.
Contact us for more information.
Adam Kondej
Research Group for the Design of Process and Control Equipment
Metals and Alloys Processing and Protective Coatings Center
Mechanical Properties of Materials Laboratory
The main area of our activity includes destructive testing methods for mechanical properties of materials and machine parts, as well as structural studies, i.e., microstructure and macrostructure. Within the scope of accreditation AB 342 granted by the Polish Center for Accreditation, we conduct mechanical, tribological, and structural testing of metals and alloys.
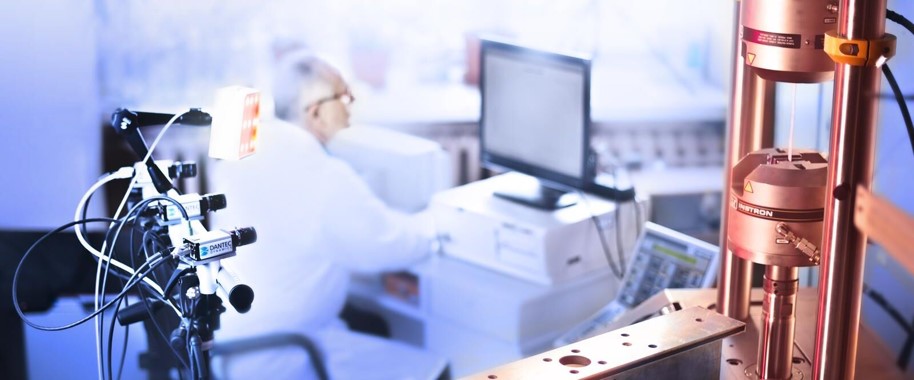
Conducts testing of metal and composite products, constructional and functional materials, in fields including:
- Mechanical testing: Testing mechanical properties Rp, Re, Rm, A, Z in a static tensile test at room and elevated temperatures, susceptibility to plastic deformation (bending test, wire bending test, Erichsen cupping test), hardness testing by Vickers, Rockwell, Brinell, microhardness by Vickers;
- Metallographic testing: – Revealing and analyzing the microstructure of metals and alloys (qualitative and quantitative structural component analysis), determining decarburization depth by microscopic and hardness method, determining coating thickness by microscopic method, determining diffusion layer thickness by hardness distribution method;
- Chemical testing: – Analysis of chemical composition using optical emission spectrometry with spark excitation.
Accreditation certificate no. AB 342 issued by the Polish Center for Accreditation
Research Infrastructure and Equipment
-Pit furnace for regulated gas nitriding Model NX-609 by NITREX
-Vacuum furnace with high-pressure gas cooling type 12.0VPT-4035/36HV
-Vacuum carburizing furnace with high-pressure gas cooling type 15VP-446
-Cryo-Temper freezer by DMP,
-Continuous furnace by Birlec
-Silite pit furnace AKS-25
-Vacuum furnace with oil cooling RVFOQ-424
-Endothermic atmosphere generator G-21
-Fluidized bed furnace FP700
-Fluidized bed furnace FP900
-Atmospheric pit furnace GOAT-1200/24
-Atmospheric pit furnace GOAT-1200/24-D
-Atmospheric pit furnace GOAT-950/24
-Atmospheric pit furnace GOAT-700/24DS
-Electric pit furnace GO-600/12
-Tempering furnace WILD BARFIELD
-Electric pit furnace GO-600/12
-Electric pit furnace GO-600/18-D
-Pit furnace type PWAF-1000-G
-Atmospheric tube furnace Type PRAT-950/10
-Atmospheric furnace GOAT-1200
-Quenching coolant tester type OG-01A
-Laboratory vacuum furnace LPP-1
-Horizontal furnace type JON-800/600-HH
-Ultrasonic flaw detector OLYMPUS EPOCH 1000
-Eddy current flaw detector OLYMPUS Nortec 500D
-WIROTEST 1000 device for non-destructive eddy current testing
-WIROTEST M1 device for non-destructive eddy current testing
-Ultrasonic thickness gauge OLYMPUS 38DL PLUS
-WIROTEST 302 device for non-destructive eddy current testing
-WIROTEST 401 device for non-destructive eddy current testing
-WIROTEST M2 device for non-destructive eddy current testing
-Hardness tester DuraScan-70
-RIGAKU PSF-3M Analyzer.
-Raman Spectroscope
-JEOL JSM-IT100 Scanning Electron Microscope with ISIS-300 attachment
-X-ray diffractometer Anton Paar - XRDynamic 500
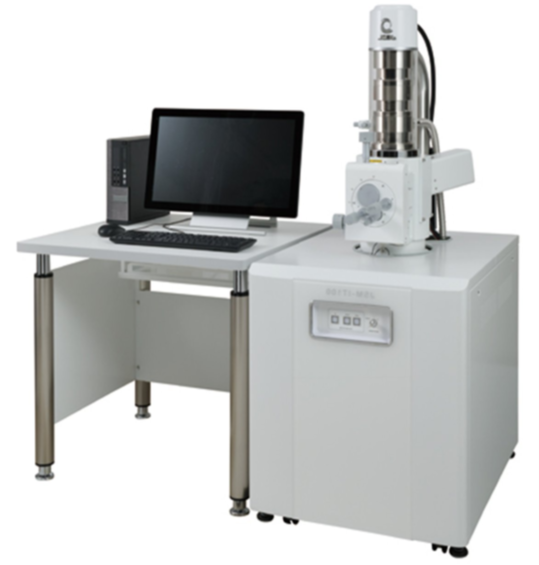
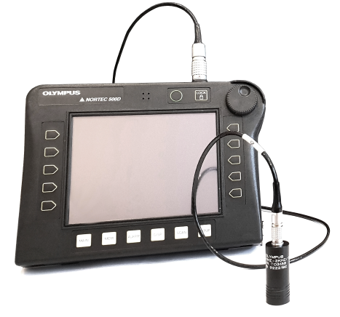
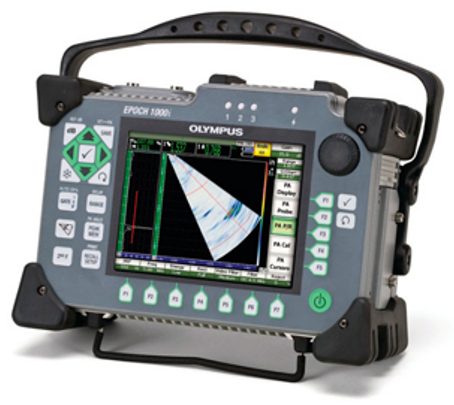
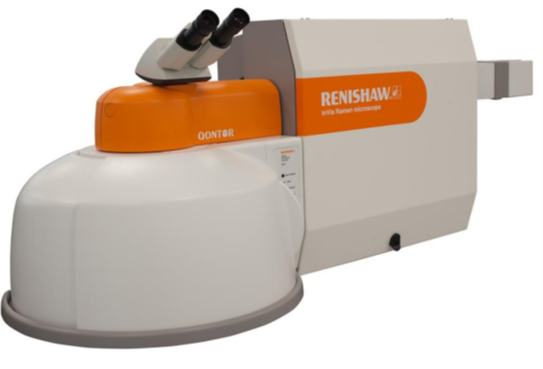
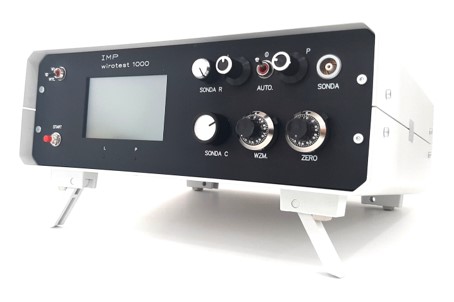
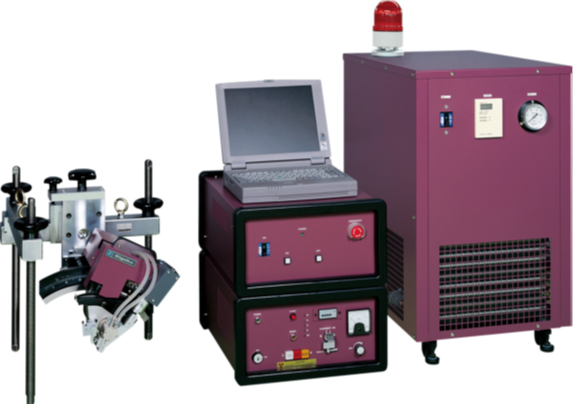